First produced in the 1800’s, today carbon fiber is used to manufacture a vast array of products, from lightbulbs to race cars to (most recently) drones. Why? What’s so appealing about the material that it’s chosen time and again over alternatives such as steel?
The Evolve 2 from XDynamics has effectively perfected the creation of this strong material to provide a drone that goes beyond industry standards for aerodynamics, with unmatched quality, and aesthetically pleasing design. Understanding why we chose to use carbon fiber for our drone requires an examination of this dynamic aerospace material’s primary characteristics and manufacturing procedure.
For the Nerds – WHAT IS CARBON FIBER
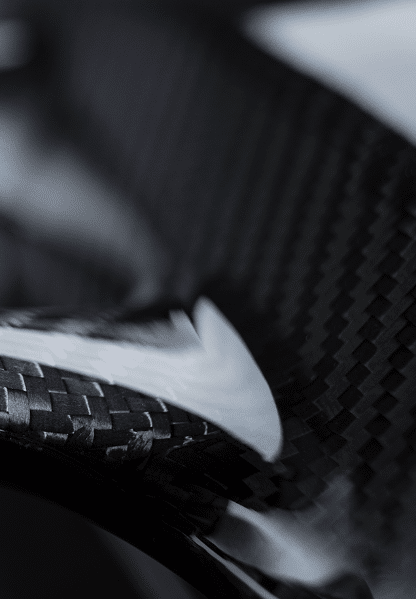
Carbon fiber (AKA graphite fiber) is a polymer made up of carbon atoms. These atoms are bound together with crystals during the manufacturing process and measure between five to ten micrometers (0.0005 to 0.010mm) in diameter.
The fibers are woven into single sheets that are flexible and have a plain or twill weave pattern. It is positioned over a mold and molded into the design while making hardware. Because it may be molded without any structural support, it is very flexible.
The EVOLVE 2 Drone Carbon Fiber Body is an avant-garde unmanned aerial vehicle (UAV) that boasts a sleek and modern design made of carbon fiber. This material is known for its strength, durability, and light weight, making it the perfect choice for a drone.
Carbon Fiber: A Brief History

The 787 Dreamliner (Pictured ABOVE) is the most fuel-efficient airliner to date and is the first airplane in the world to be mostly made of carbon fiber. It comprises around 35 tons of carbon fiber reinforced plastic.
Joseph Swan, an English scientist and chemist, was the first to create carbon fiber for use as the filament in light bulbs in the late 1800s. Thomas Edison invented the pyrolysis method in 1879 and used it to produce carbon fiber. Edison produced the fibers by carbonizing bamboo slivers and cotton threads at very high temperatures.
Light bulbs were made of carbon fiber because of the materials exceptional heat tolerance, which prevented the filaments from degrading while transmitting power. Although the pyrolysis method is still used to generate carbon fiber today, different materials are being employed to produce a product that is stronger and superior to bamboo.
Researchers discovered that carbonizing rayon created higher-performance carbon fiber throughout the 1950s and 1960s. However, rayon only contained 20% carbon, which rendered it too flimsy for the researchers’ tastes even when heated. When they switched to polyacrylonitrile (PAN), which has a carbon content of 55%, things went better.
This eventually led researchers to begin heating and carbonizing petroleum pitch derived from oil processing. This yielded 85% carbon and outstanding strength. Over time, carbon fiber production has improved to develop stronger yarn. Aerospace companies, such as Boeing, Airbus and McDonnell Douglas and of course XDynamics have all transitioned to carbon fiber.
How carbon fiber is made and how we do it
The four steps of carbon fiber production are stabilizing, carbonizing, surface treatment, and sizing. The fibers are heated to 590 degrees Fahrenheit for 30 to 120 minutes as part of the stabilizing procedure. During that time, the fibers draw oxygen molecules and reorganize their bonding patterns to establish a stronger, more robust foundation.
Following stabilization, the fibers are heated at extremely high temperatures between 1,830 degrees Fahrenheit and 5,500 degrees Fahrenheit. The characteristics of the finished carbon product are directly influenced by the exact temperature. Carbon is often stronger when heated at lower temperatures than when heated at higher degrees, which generally allows for more elasticity.
In either case, a furnace devoid of oxygen and filled with gas mixtures is used to heat the carbon fibers. These mixes remove non-carbon atoms and strengthen the crucial connection between carbon crystals when coupled with high heat. The crystals then line up along the fiber’s long axis.
The fibers are coated with epoxy, polyester, nylon, or urethane during the sizing process before moving on to the final stage of weaving. After weaving, the fibers are wound into cylinders known as bobbins, which are then fed into a spinning machine to produce yarns from the fibers.
Finally, a single sheet of carbon fiber has been woven and is prepared to be moulded onto its intended use—a product. Carbon fiber for the Evolve 2 is made from a single sheet that is shaped to create the drone’s Monocoque Chassis. The entire procedure entails 26 steps and can only be finished by qualified technicians who are well aware of the exacting standards needed for an XDynamics drone.
Understanding Monocoque Construction

The greatest supercars in the world served as some of the design inspiration for the Evolve 2, and the manufacturing process is surprisingly close. French for “single shell,” monocoque is an ideal way to describe what monocoque construction stands for.
Most importantly, monocoque constructions are stiff and difficult to bend, but surprisingly light. This makes carbon fiber an ideal choice for high-performing vehicles, airplanes and drones.
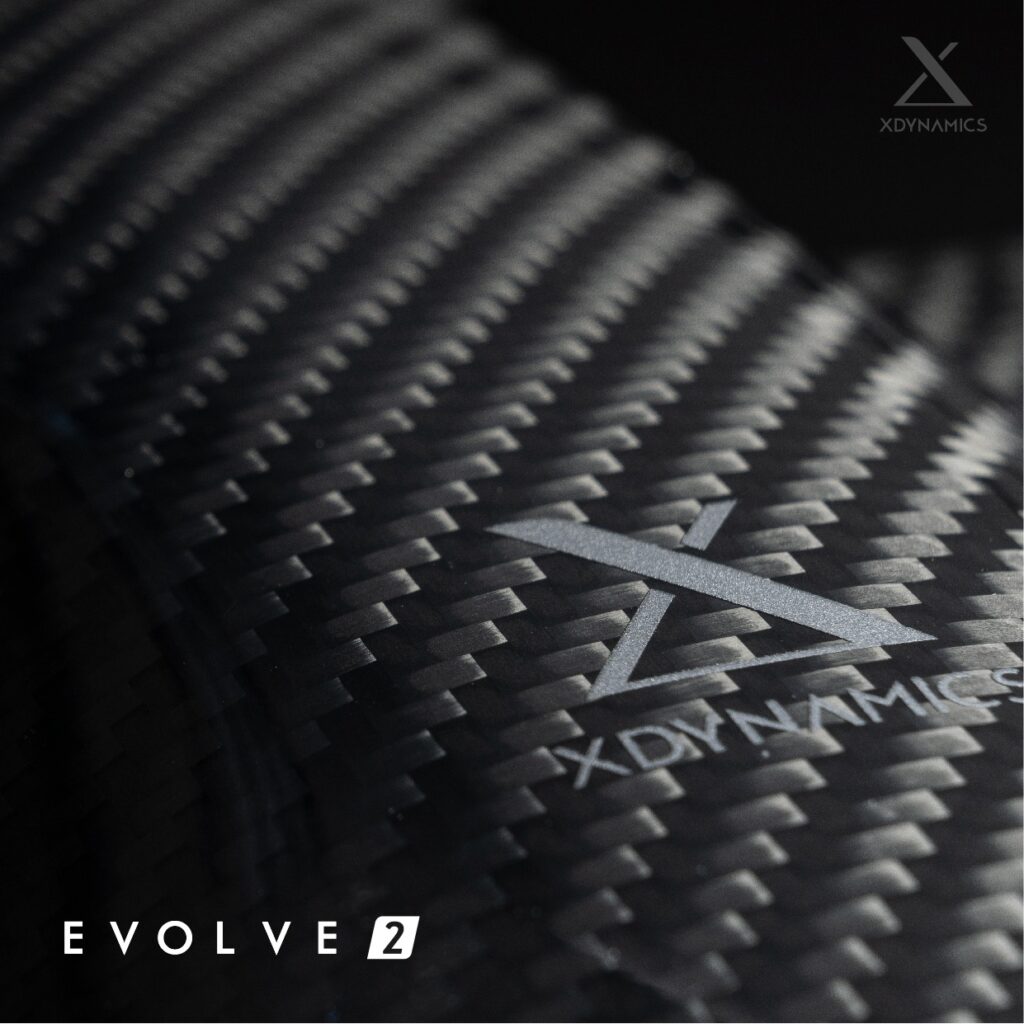
Carbon fiber is woven into a sheet with a plain or twill configuration. While they both have their own unique advantages, in the vast majority of cases, twill offers significant advantages for products with complex design.
Twill is generally formed in a 2×2 or 4×4 format. Each section on the sheet is called a tow. In a 2×2 format, two tows pass over followed by two tows passing under. Similarly, a 4×4 twill has four tows that pass over and under others.
1K, 3K, 6K, More
The “K factor” of a sheet is the quantity of carbon filaments in each row. The standard is listed as 1K, 2K, 3K, 6K, 12K, etc. on spec sheets and marketing. For instance, there are more than 3,000 fibers in that row of carbon fiber with a K factor of 3K. The k factor affects the material’s strength, weight, and malleability. To be clear, a higher number K rating does not equate to better or worse material. The K factor that is finally selected should be based on the final product design and its intended function.
The most common choice, 3K carbon fiber, provides a great combination of characteristics. It is sturdy for prolonged usage while still being malleable. Comparatively speaking, 3K carbon fiber is stronger than 6K, 9K, and 12K. The K factor affects material weight as well.
A Deeper Look at our EVOLVE 2
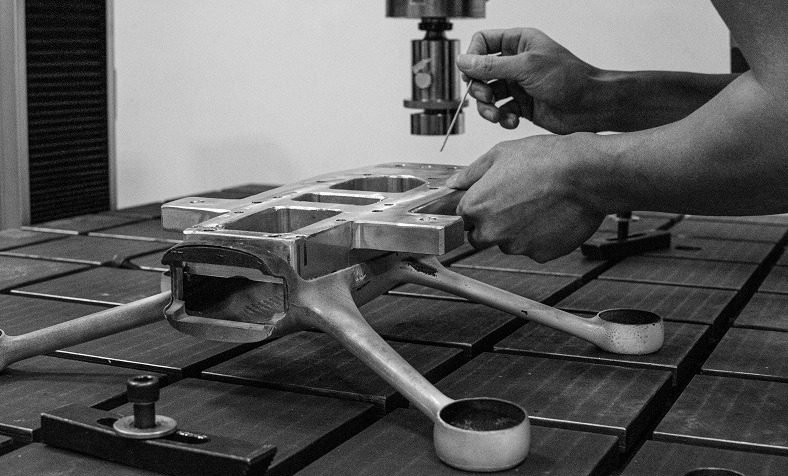
When designing Evolve 2, XDynamics particularly used carbon fiber in an effort to enhance and perfect the architecture and aerodynamics of the drone platform. By doing this, the Evolve 2 satisfies and surpasses industry standards in even the most difficult flying scenarios.
For professional drone pilots who want durability and a smooth flight, the Evolve 2 is the best platform. Even under the most challenging flying circumstances, the Evolve 2 is safeguarded by the carbon fiber chassis’ robustness. Additionally, its anti-ultraviolet qualities shield it from harm caused by prolonged sun exposure. Compared to its heavier steel equivalent, its reduced weight also allows for nimble turns and extended flying periods.
In sharp contrast to and with a major advantage over plastic competitors, the Evolve 2 makes a statement both in the air and on the ground thanks to its blend of sportiness and beauty through craftsmanship of the highest aerospace materials.